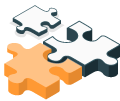
Growing demands for plant customization and shorter construction times constrained by rising quality standards are the main drivers of desalination engineering today.
Construction of mega-plants may be roughly subdivided into two equal-duration parts - assembling and commissioning of equipment and systems.
How digitization changes the commissioning of mega-plants has been discussed in the article "Plant Commissioning: Data Tsunami".
Management of onsite assembling of equipment and systems is a new topic in desalination. Actually, it is the top of the assembling science iceberg, hiding beneath the water design for assembly, design of assembling instructions, assembling quality assurance, and the assembling metrics. (Concrete works are not on the list as they are part of assembling.)
The criticality of design for assembly may be illustrated by an evolution of the reverse osmosis membrane stand designs marketed by IDE Assets since 2004.
Design A was expensive in manufacturing as every membrane vessel is connected to a feed distributor made of costly alloyed steel but it was easy to assemble in the field. Design B was used in the Sorek 1 desalination plant. It was expected to be less expansive than design A but it was only marginally. In addition, assembling was too complicated and time-consuming. Despite its ugliness, design C stacked of identical skids moves the problems of assembling from site to factory and slashes down the construction time. The assembling sequence does not change with the plant size (but the stack height does).
The design of assembling instructions focuses on a sequence of the assembling steps requiring the least experience, time, and tools. The assembling metrics try to find a link between the assembling method and the final product reliability.
When it comes to documenting the assembling requirements, companies consider hiring experienced site supervisors a better alternative.
The value added to the project covers inspection of materials and workmanship, monitoring compliance with the assembly good practices (not documented unlike instructions), and registering daily progress.
All these points constitute tacit knowledge that vanishes at the end of the project. To capture this knowledge and make it accessible to everyone is the task of digital management.
It is a serious competitive advantage today when more and more experienced employees are retiring while fewer skilled workers are coming on board.
Documenting of the plant assembling starts with the following three points.
- sequence of steps
- step outcome acceptance criteria
- time needed for each step
For procured equipment, the first two points are touched on in the manufacturer's operation and maintenance manual. What is inside can hardly be called detailed instructions - rather general recommendations - as the focus is on how not to damage equipment during installation.
The described above was the starting point for crenger.com's development of the plant assembling management framework. It views the plant as a hierarchy of assembly parts and sequences.
Its core is the assembling sequence editor. At the basic level of the above-mentioned hierarchy, its input is an assembling or layout drawing of an equipment piece or a system. If the drawing is generic it has to be linked to a selector targeting all the objects in the generic class. If the drawing is specific, it is directly linked to the P&ID item or group, or the plant plot area.
Next, the object is subdivided into essential parts. Finally, the steps are created of parts and the action verbs like "install", "connect", "check", "inspect", etc.
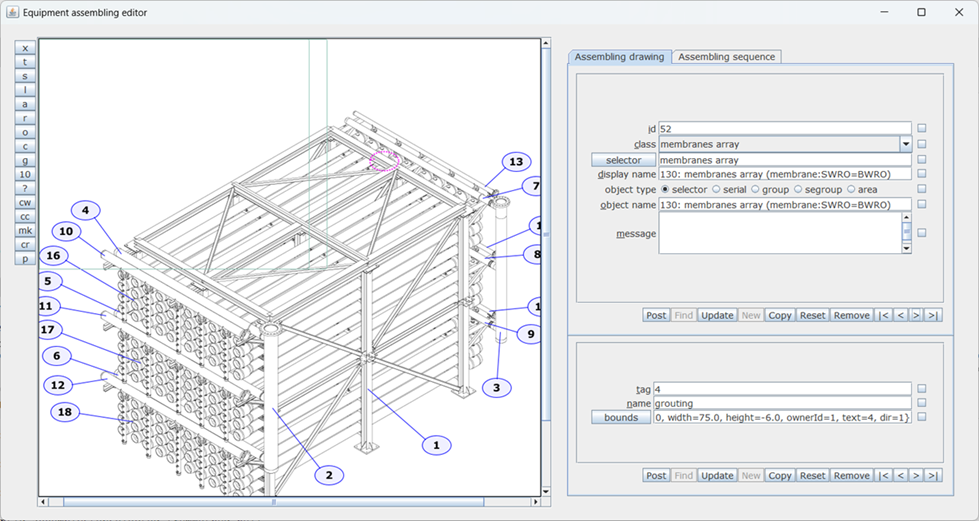
At the higher level, the assembling sequence editor builds sequences of steps linked to lower-level sequences instead of parts (and the "execute" verb). The top sequence is the plant assembling from assemblies like intake station, pretreatment, reverse osmosis, and posttreatment.
After the assembling steps are loaded with the work hours and attached to the named resources, the assembling sequences may be turned into the assembling schedule.
Online reporting on the assembling progress is a two-step process. The subcontractor selects the assembling step connected to an object on the plant P&ID or wiring diagram and then fills in the data on its current status.