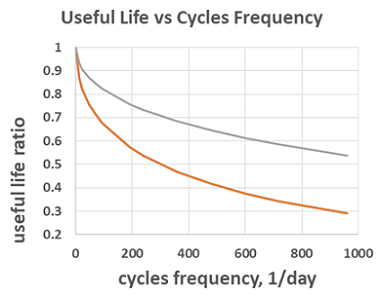
ASME Boiler and Pressure Vessel Code (Section VIII, Division 2) defines fatigue as “… conditions leading to fracture under repeated or fluctuating stresses having a maximum value less than the tensile strength of the material". Bending the wire back and forth about a point until failure is a common example of fatigue.
Cyclic fatigue accelerates the failure rate of equipment and decreases its useful life. It is triggered by periodic unloading-loading of equipment or swings in the fluid working pressure in batch processes. Cyclic fatigue accompanies broader phenomenon called transient performance.
The bigger the amplitude and the frequency of the load (pressure) change, the higher the fatigue rate is. Its absolute value over time depends upon the conditions of operation and may be described by the red curve of the graph. (This curve may be obtained from S-N curve normally used for cyclic fatigue prediction.)
It plots the useful life ratio against the cycles' frequency. The case of frequency = 0 corresponds to the useful life predicted for the static design conditions lasting infinitely. In practice the robustness of design is defined by the pressure class like PN16 or ANSI #150 or piping schedule.
The red curve approximates the data for super-duplex piping of class 600 – energy recuperation pressure vessels - from operating plant of 410 MLD.
Unexpectedly fast aging of the vessels is a result of compound effect of biofouling induced corrosion enhanced by high seawater temperature, surface quality, energy recuperation generated cyclic loads, and water hammer.
As follows from the red curve, with energy recuperation at 2.5 minute per cycle (576 1/day) the useful life of pressure vessels is just above 30% of the expected one at the static load. In other words, cyclic fatigue substantially increases CAPEX of the system.
How to combat the cyclic fatigue? Simple and effective solution is overdesign. Increase in the pressure rating (say from #150 to #300) not only raises the static useful life (point where frequency = 0) but decreases the amplitude of the pressure swing.
Practical cases of cyclic operation
Ultrafiltration. It is a core process of seawater pretreatment systems. It is not continuous - a batch one requiring backwash every 0.5 – 1 hour. At the frequency of 25 – 50/day the UF elements go through the full pressure range from operating one to zero. In addition, fast closure of the pneumatically actuated isolation valves produces series of water hammers. Harsh operating conditions necessitate periodic integrity tests – part of UF operating and maintenance procedure. Such systems shall have overdesign of 200%. Large-capacity UF shall be equipped with water-hammer mitigation devices.
Desalitech batch BWRO desalination process. During the cycle no brine flow exits the BWRO membrane array. It is recirculated, the decrease in its volume being compensated by adding fresh feed water. The process ends at the maximum pressure. Then the pressure decreases to minimum and the brine replacement with fresh feed starts.
Working at approximately 140-160 1/day (the author estimate) and full pressure swing, this process requires some overdesign. Judging by its catalog of 2017, the company is well aware of cyclic operation consequences. The mentioned catalog offered the same mechanical design rated at 31 Barg for 3 configurations differing in the maximum feed pressure – 13, 19 and 26 Barg. First two have substantial overdesign. It is not clear whether the last one is the result of the design fine tuning or deliberate trimming away the expensive longevity.
(I am convinced this company amassed the biggest data on cyclic fatigue phenomenon in desalination. What makes me think so? Because actually I made some tiny contribution to it in its early days. Why not to make this data public? )
ROTEC BWRO desalination with flow reversal. Flow Reversal is a batch process, in which the flow direction of the feed stream in BWRO pressure vessel arrays is periodically switched over. The company does not share information on the frequency of switching but says that it is defined by the scale growth rate. (If we use it as a basis for the cycle duration estimation, we may arrive at 20 minutes per cycle or more.)
By the same criteria, Flow Reversal may be classified as the cyclic process with relatively low amplitude of the pressure change compounded by micro- water hammer. My opinion is that 20% overdesign is a good negotiating point in conditions when the information about transients and design details is hidden.
MAXH2O Pulse Flow BWRO desalination of IDE Technologies. To create pulses the incoming feed flow is interrupted by periodic closure/opening of the valve installed at the BWRO membrane array outlet. The company brochure explains that "..brine flow discharges as pulses in a very short time at the maximum flow allowed by the membrane manufacturer… The flow is not stable, and the osmotic and gauge pressure change frequently and rapidly."
This paper throws more light on the design and operation details. For instance, tested cycle durations were in the range of 60 – 200 sec. These figures correspond to frequencies of 430-1440 1/day. Let us not forget that pulse generating valve generates water hammer as well. The company says nothing about this "companion".
Mere comparison to Desalitech frequencies of 140 – 160 is enough to raise a red flag in negotiating the warranty conditions and operation and maintenance schedules and tests (like integrity test).
Variable-load desalination. The seawater desalination plant may be effectively engaged in the peak shaving - the reduction of the amount of electricity drawn from a power utility during utility designated peak time periods (Palmachim, Israel). In this mode of operation the plant doesn't produce water during noon peak hours when the electricity tariffs are the highest. The capacity of the desalination plant operated in such a mode has to be bigger by at least 10- 15% %, and the plant shall be designed at least for 300 startups annually. The last figure suggests that the plant critical systems be overdesigned by at least 20 – 30%.