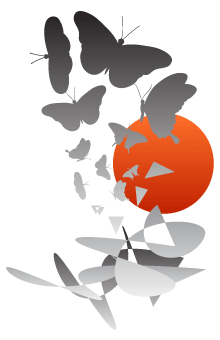
Probably the simplest way to define disaster is through comparison with the project uncertainty - the well-acclaimed category in the management theory.
Project uncertainty is when we know the destination but we are uncertain about the best route to arrive there. Disaster is when a well-known route beaten many times is suddenly blocked by an unexpected event. Disaster is an uncertainty unknown in advance. While uncertainty is associated with a lack of knowledge, disaster - with an outburst of chaos.
Chaos has nothing to do with the probabilistic distribution of repeated measurements miraculously regressed to the mean and, therefore, fitting nicely into the rational and deterministic model of the world enshrined in the minds of engineers.
Chaos theory proves that even the strictest rules and overarching information won't guide you against unpredictable outcomes. The consequence is no matter how perfect your IT technology is, the perfect execution of a megaproject is an unreachable goal.
Chaos is a synonym for the irrational hidden behind the "Force Majeure" and "Act of God" paragraphs in the project contracts.
The megaproject's complexity and size increase the risk of disasters related specifically to the project procurement phase. Returning back on track after the disaster is time-consuming and often expensive too.
To select the best way to deal with disasters, crenger.com enhanced the project scheduling framework with the Random Disaster Generator (RDG). It fits perfectly with the "regression to the tail" law observed by Prof. Bent Flyvbjerg in failed megaprojects. Maintained by his team the registry of megaprojects executed in different sectors (energy, construction, water, IT, transportation) includes thousands of entries.
Multiple runs of RDG on the project schedule produce the output needed to
- cut the disaster distribution tail - by adding an extra time buffer to the project schedule,
- extend and enhance the force majeure provisions with the specific cases of the contract failure.
Depending on the project size the reasonable time buffer varies between 2 and 6 months. The project delivery provisions should be flexible enough to accommodate the force-majeure cases in the long-lead equipment procurement.
The current version of RDG has been tuned to the disaster cases observed in real megaprojects. Below is an excerpt from the disaster registry maintained by the author. All the manufacturers are well-known in their market segments.
#1
During the site test of the media filters the flap valves failed. It was found that the valve manufacturer scaled up the design without validating the valve's mechanical characteristics. The valve re-design and repair added up over US$1 million to the project budget and 3 months to the project schedule.
#2
During the factory test of the product pump delivering 1200 cu.m/h at 30 Barg a high vibration level was witnessed. After investigation, it turned out that the actual pump BEP was at the flow 80% bigger than the requested one. Settling the dispute and the third-party consultation added 3 months to the pump delivery schedule. The pumps were never repaired.
#3
The pump of 500 kW (main service) did not pass the factory test due to mechanical seal leakage. It was admitted by the manufacturer that the seal was selected regardless of the pump peculiarity - It was for vertical installation. Investigation into the problem, procurement of new seals, and witnessed test added 4 months to the pump delivery schedule.
#4
AC motors of 800 kW (main service) ordered from a very reputable company did not pass the standard type test. It turned out that the rotor material composition slightly differed from the specification. All the motors were replaced with new ones and witness-tested. It added 5 months to the pump delivery schedule.
#5
After the plant acceptance test, the AC motors of 6 MW (main service) exhibited accelerated wear and tear. On investigating the case, It was found that the motor frame was designed not rigid enough. The reason was the limited experience of the manufacturer in the large-size motor design. All the motors were dismantled, sent back to the factory for repair, and re-installed again.
#6
The rotodynamic analysis of the vertical intake pump showed a high probability of vibration surpassing the acceptable maximum. It turned out that the actual motor weight (used in the analysis) was bigger than the one given in the pump specification. Selecting the best alternative for the problem resolution and re-inforcing the motor stool added one month to the pump delivery schedule.