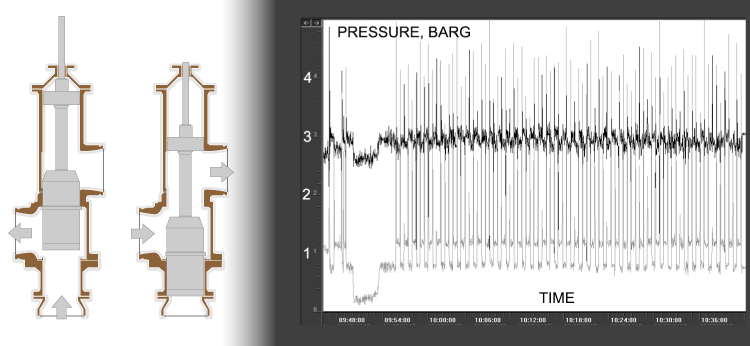
This is a rare case where theory of water hammer meets practice. It describes the DWEER-controlling valve inherent performance in ideal test environment.
Problem
A company designed a new valve with an intention to market it. Its operation principles were similar to LinX valve of Flowserve used in Dual Work Exchange Energy Recovery device (DWEER). Today DWEER is a synonym of a piston isobaric energy recovery device using positive displacement due to its wide application in seawater reverse osmosis desalination.
This valve was claimed to have smaller leakage. To test the operability of the valve high-pressure end a simple closed-loop test-bench had been assembled. All attempts to run the loop at the valve trim travel velocity of 100mm/sec and 1 cycle/minute had the same ending - after 2 days the pipe burst at the same point located at the far end of the straight run of 15m. Checks of the mechanical design pressure yielded nothing - it was slightly below the pump shut-off pressure of 3.2 Barg. Hydraulic resistance of the line was negligible - water velocities were below 2.2 m/s. The PVC pipe pressure rating class was SDR33 or 3.2 Barg. In accordance with ANSI/AWWA C950-88 this pipe should withstand a transient pressure increase of 1.5 times the design one. What is the reason of the pipe burst?
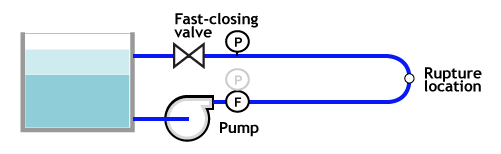
Procedure
After verifying the pump performance, my first step was to move the pressure transmitter to the valve inlet. The obtained data on the pressure revealed high oscillations reaching 4.5 - 4.9 Barg (shown above). Clearly it was a water hammer occurring nearly 3000 times (!) before the pipe burst.
The second step is to build a hydraulic model from generic hydraulic elements described in Applied hydraulic transients (Chaudhry M.H. 1979). This book is extremely popular; all the water hammer prediction programs available in the market use its equations and algorithms.
As the tested valve performance characteristics were unknown, it was replaced with the butterfly valve with known pressure loss against the valve trim travel function.
Once the hydraulic model is built, it should be tested against the real operation. The numeric calculation procedure from Chaudhry is based on the finite difference technique - characteristics method - where pressures are computed along the pipe for each time step. So pressure may be predicted for any location at any time.
Table 1. Calculation summaryCategory | Units | Closure 0.7 sec | Closure 0.4 sec |
---|---|---|---|
INPUT | |||
Pipe material | PVC | PVC | |
Seawater mass flow rate | kg/s | 270 | 270 |
Inlet pressure | m | 24.5 | 24.5 |
Piping internal diameter | m | 0.4 | 0.4 |
Piping thickness | m | 0.025 | 0.025 |
Total piping length | m | 30 | 30 |
Valve closure time | sec | 0.7 | 0.4 |
Distance to the point | m | 15 | 15 |
OUTPUT | |||
Fluid velocity | m/s | 2.088 | 2.088 |
Celerity | m/s | 1284.72 | 1284.72 |
Maximum pressure | Barg | 4.553 | 5.652 |
Maximum pressure location | m | 29.67 | 29.67 |
Maximum pressure time | sec | 0.177 | 0.137 |
Minimum pressure | Barg | 2.42 | 2.416 |
Minimum pressure location | m | 29.02 | 29.02 |
Minimum pressure time | sec | 0.0005 | 0.0005 |
Distance to pipe bend | m | 15 | 15 |
Pipe bend maximum pressure | Barg | 3.85 | 4.45 |
Pipe bend maximum pressure time | sec | 0.286 | 0.167 |
Pipe bend maximum pressure rise | Bar/sec | 19.87 | 38.4 |
Point maximum pressure rise time | sec | 0.034 | 0.034 |
Findings
- Maximum pressure of 4.55 Barg is reached after 0.18 sec of the valve closure start, 0.3 m upstream of the valve.
- Maximum pressure of 3.83 Barg at the rupture point is reached after 0.29 sec of the valve closure start.
- The pump presence increases the above values by 0.3 - 0.35 Barg only.
- Quicker closure of 0.4 sec raises the peak pressures to 5.65 Barg.
- As follow from the pressure histogram, the measured peak values are below 5 Barg - in good agreement with the prediction.
Material fatigue caused by water hammer induced pressure oscillations (pressure rise of 19 - 39 Bar/sec!) is the reason of the pipe burst. The only possible solution is to install the surge suppressor - the air- filled vessel adjacent to the valve.
You ask what about the valve? It never became a competitor of Flowserve LinX. It turned out that "higher leaks" were a touch of genius to keep the water hammer at bay.