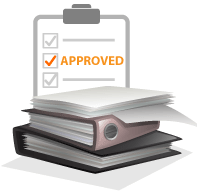
All inspections seem routine and boring. To me, boring is a magic word because it always leads to some bigger challenge – a perfect topic for digitization. Incoming goods inspection is not an exception - it is equally important for megaprojects execution, the plant operation, and its maintenance.
Incoming Goods Inspection (IGI) is the final stage of goods manufacturing inspections - a check-out before goods are entered the plant construction site.
Unlike previous factory inspections, IGI is a project schedule milestone and a condition for payment. If it is missed, the failure risk jumps up.
IGI stands out from the inspections' crowd because of the big volume of information to be taken into account and the weight of the final decision – accept or reject the product.
Every incoming goods batch undergoes the following typical checks.
- delivery bill and purchase order match
- visual defects
- nameplates, markings, barcodes
- dimensions & materials
- shipping documentation package contents
- manufacturing records book auditing
- billed quantities
- data logging
- goods release and OEM notification
Checks 3 & 4 require a comparison basis - the product specification and assembly drawings. To perform these checks some skills are needed as nameplates, markings and barcodes are not part of the specification. Neither all the checked dimensions may be found in the specification.
Shipping documents are a balance of the product submittals received before the product shipment. The original submittal schedule is part of the product specification. Before Check 5 the inspector shall audit the submittals' schedule and already submitted documents as well.
Manufacturing Records Book (MRB) auditing is the most time-consuming and difficult part. MRB is the answer to ITP – Inspections and Tests Plan described in the product specification. MRB has 4 major sections – Acceptance, Materials & Fabrication, Inspection & Test Reports, and Additional Information. They are subdivided into over 20 document types submitted for all major parts of the product. Examples are Material Traceability Records, Material certificates, Release Notes, etc. For pumps, MBR may contain above 100 pages. In reading them practical knowledge and experience matter.
Have all the tests been conducted? Has their result been approved? Do they match ITP? Does MBR contain all the relevant certificates, reports, and release notes?
Handling the burden of IGIs with the company's own staff is not possible as it is not evenly distributed in time. The practical solution is outsourcing IGIs to third-party inspectors (TPIs).
Applied Technical Services (ATS), Pro QC International, Ivy, and Eagle are some better-known examples of TPIs.
IGI digitization requirements shall include the following.
- Purchase orders, specifications, OEM submittals, inspections, and the test results search
- Automatic checklist generation
- Possibility for OEM to upload parts of MRB before products shipment
- Possibility for OEM to have online access to the IGI results
- Possibility to view NC reports online once the product is rejected
- Possibility of an auto-acknowledgment of the successful goods' acceptance