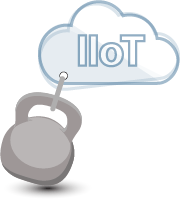
Industrial Internet of Things (IIoT) growth is staggering – 18.6% CAGR. According to forecasts, in 2020 the IIoT market will reach nearly US$ 140 billion.
Undoubtedly, this phenomenon will transform every industry (Power, Oil and Gas , Pharma and Water) and change the way companies execute infrastructure and process projects today.
What is apparent now is that EPC contractors and engineering service providers have not yet figured out how to leverage the power of IIoT, how to improve industrial control systems and adapt them to an expected surge of rich data.
Most experts consider predictive maintenance as a main domain of IIoT. To me IIoT is a precursor of transition to remote and fully automatic plant operation, to substantially safer designs, and to more flexible operation.
To unlock its full potential, IIoT has to deal with a few challenges.
1. Control design robustness and reliability are not a priority of EPC projects
HSE research published in their book 'Out of Control', shows that 60% of all process industry accidents can be traced back to errors in the control design and specification.
Operators of big desalination plants are trained to make operational decisions under pressure of the whole plant shut-down, which with better and smarter control may be totally avoided. (Such a control requires more man-hours by a factor of 4!)
Another reason of operator errors is bad timing for the HAZOP study relying heavily on the control implementation. Ironically, in all cases known to me, HAZOP was conducted long before the mentioned implementation.
2. Control design is considered one of the project risks today.
How serious is this problem? In 2008 I participated in the megaproject in which control and instrumentation design overruns hit 500% (!) - close to 50% of the engineering budget - and caused several-month delay. The reason was a mismatch between the client expectations regarding the plant functionality (redundancy, fail-safe logic, on-fail sequences, etc.), and the control practices adopted in water industry.
3. Good control strategy and design for reliability beat expensive instrumentation
Adding extra instrumentation always decreases total reliability of the system and makes maintenance more complicated (more calibration procedures, manual operation checks and local gauge instrumentation).
Ways to be found to understand this trade-off, to reduce downtime, maintenance costs, to rationalize data mining, business analytics, and transition to predictive maintenance. Will the plant operator be ready to share the IIoT data with the project contractor in other then win-win situations?
4. Complexity of the PLC programming (process and sequence controls and data acquisition) does not allow to accommodate the rich data volume growth.
The bigger the plant, the more signals and events shall be processed by the PLC software - SCADA program. As shown in the table below nearly 12000 parameters shall be coded into sequence/logic control manually! The SCADA program validation is not automated and takes many weeks of hard work. Debugging may take 6 – 12 months!
Table 1. 150 MLD SWRO desalination plant control metricsNo | Control event category | Quantity |
---|---|---|
1 | Commands (to open, to close, to start…) | 2350 |
2 | Alarms & States (high, open, closed, running) | 9100 |
3 | Interlocks (safety and operational) | 520 |
The first strategic step towards ultimate solution of the above-mentioned challenges - auto-generation of the PLC software - is to bridge the gap between the P&ID and SCADA development (mentioned in previous article). And the starting point is the specification and framework for Functional Design (FD) requirements. Actually, FD is an extension of Design Thinking.