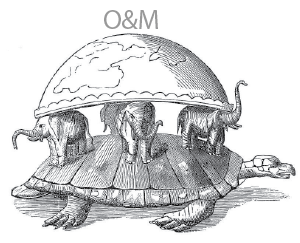
Design reliability, as any science overloaded with rusty old problems, is aging. It does not guide engineers through the intricacies of the megaproject engineering. But it should, as reliability is a fundamental property of any commodity. Digital transformation we witness today is a perfect time for rehashing our knowledge on reliability, changing our engineering priorities and re-focusing our businesses on what is critical for digital acceleration.
The following situation best describes the current status of the design reliability practices.
Recently I got a call from the agent of the original equipment manufacturer. Its equipment has been installed and in continuous operation over 7 years in one of the biggest desalination plants.
The agent explained that the reason of the call is the request from the plant operator for the broken parts replacement. He described the character of the failure and asked the cornerstone question - "May this failure be classified as the equipment defect or not? Would it impact the reputation of the company?"
As I had been involved in the design of the subsystem in question, I calmed down the agent saying that it rather seemed like due to the negligence of the plant operator.
This situation is a direct consequence of broken relationships between the equipment manufacture and the plant operator. The equipment manufacturer does not have feedback from the plant operator, needed for the design improvement because the operator is afraid that the O&M faults and negligence cases will leak out.
No feedback? Get "one-size-fits-all" warranty for all the customers – dumb or smart, from water utilities or oil and gas.
On the other hand, the O&M misses and faults are inevitable given the amount of the preventive maintenance tasks to be executed. For the 100MLD desalination plant it is well above 800!
Personally I consider this situation troublesome by another reason.
The plant operator directly talked the manufacturer instead of talking to the plant designer - just to validate the engineering guidelines for the equipment selection.
This Vow of Silence has its toll; it is next-to-impossible to get the reliability data from the manufacturer. So "the equipment design shall be reliable" sentence is common in the technical specifications for the equipment ordering.
The paradox is that specification datasheets do not even contain entries for the reliability data. As a result, project engineers do not have formal basis for negotiating the reliability and maintainability with the equipment manufacturers.
The reason is not the lack of theoretical knowledge, but of the established framework for collecting, processing and storing the feedback from the plants.
It suggests mutually beneficial collaboration between designers and operators. Instead petty bargains prevail: ordering spare parts through the engineering company makes them 15 -20% more expensive.
They hide a real gem of the problems where design reliability shines – different rate of the equipment pieces depreciation. In practice, the life expectancies range from 2 to 30 years. This disparity always leads to unexpectedly high revenue losses (I will discuss reasons elsewhere).
The Bermuda Triangle situation is a direct consequence of the human factor at work.
Design for reliability is not possible without mending relationships between the stakeholders - manufacturers, operators and designers.
Albert Einstein is quoted as saying – "We cannot solve our problems with the same thinking we used when we created them". I would add – non-digital thinking constrained by data-deficit dogmas.
Digital thinking is born of the information transparency and abundance laws. And the first step is for the plant designer to assume responsibility for the preventive maintenance tasks definition, and the execution surveillance.
Today the first task requires around 1000 man-hours. Crenger.com makes it ZERO. In fact, Crenger.com turned it into part of the design process and the plant warranty conditions.
The second task is where the magic begins. The steady stream of operation and maintenance information "wrapped" into natural context of design specifications and guidelines will be used for screening the nuggets of the design reliability and decision making.
With the information stream available, to make the dream come true the specifications and design guidelines shall be digital. How to do it? Learn from Crenger.com.