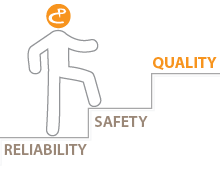
To many of us the quality wisdom is condensed in a single phrase: "The bitterness of poor quality remains long after the sweetness of low price is forgotten". Quality is an emotional trigger that sharpens our memories and ability to learn from mistakes.
By McKinsey (2017), 98% of infrastructure projects suffer cost overruns of more than 30%; 77% are at least 40% late. Study does not say anything about the quality of the project execution. But we can assume that quality - conformance to the project requirements - follows cost overruns and delays.
The notorious case is Ashdod desalination plant (Israel, over $380 million), where cost overruns and delay hit 75% and 100% accordingly. To make matter worse, faulty construction and engineering of this grass-root plant limit its current capacity to no more than 85% of what it was designed for and what its license terms require. As a result, the plant is expected to lose about $9 million a year, rather than earning money for main contractor.
My only explanation of the above-mentioned faults is a lack of proper Quality Management System (QMS), which principles and requirements are set forth by ISO 9000 and ISO 9001 standards. But here is a catch: these standards are for companies, not big projects executed in collaboration by a number of contractors.
In 2003 I participated in a mega-project without any QMS; instead the project team included experienced engineers with QMS knowledge built into their culture and expertise.
So it is perfectly legal not to set any QMS at all and instead delegate associated responsibilities to the project supervisors. In fact, over 99% of US companies are not ISO 9001 certified and not following ISO basic commandments. (Statistics is silent about which QMS if any these companies are using.)
On the surface, the no-QMS approach has a number of pros - less engineering workhours and shorter schedules and leaner budget. The only disadvantage is sky-rocketing risks of quality-related issues like faulty manufacturing or processes.
Undoubtedly, quality is an economic category: too good QMS will destroy the project award chances due to its high costs of maintenance. In this regard the following clause, taken from the web post of well-known RO manufacturer, seems nonsensical at all.
"As a world leader in membrane water treatment services our quality is unparalleled".
Example is the desalination units for oil rigs; compliance with higher quality API standards more than doubles their price.
Unlike cost overruns and delays, poor quality may be the company reputation instant killer; in the age of hyper-connectivity and fierce competition bad news rides a fast horse.
The network power awareness leads us to a simple starting point – QMS should be considered a primary source of the client's digital experience. In other words, it should be transparent to the client 7x24. (To be fair, the ISO standards name first the customer satisfaction in the QMS objectives.) In addition, this QMS should survive and work concurrently with endless digital transformation underway in many companies.
Before delving into other requirements, I suggest resetting our "quality" mindset to get rid of common misconceptions related to QMS.
The common belief is that QMS complements project management. In other words, QMS comes after project management. It does not. Quality is above management as building risk-preventive QMS is a lengthy statistics-rooted process that starts long before any project. Prevention over inspection is a fundamental tenet of QMS stating that quality is planned and designed into a product – not inspected and re-worked. My experience tells that the costs of risks prevention may be less than those of correcting the nonconformities, if project management is a company core business.
Without exaggeration one may say that modern project management is quality driven and quality scoped, and an extension of QMS.
Another popular gut feeling is that there exists a subtle clash between ISO standards conformity and the company core business development. Some engineering services providers say that obtaining and maintaining ISO 9001 certification may restrict a company's ability to rapidly adapt to new technologies and manufacturing methods.
Let's separate wheat from chaff. The fundamental structure of QMS set by ISO 900X standards cannot be neglected; it is wisdom of huge experience gained across many industries. Being built only once, the QMS structure may be easily transposed from one project to another without re-inventing the wheel.
QMS structure cannot be substituted with the management structure detailing number of QC supervisors and engineers as the pivot of QMS by ISO standards is recording of mundane business activities. In the past it was ludicrously expensive; no contractor could afford it. Not anymore.
It is thought that the core QMS activities follow the QMS structure – they are no-brainer and stable: with a set of declarative policies and procedures any QC inspector may handle them. Nothing's far from the truth. No one alone can handle and file over 8000 certificates of completion for desalination plant of 150 MLD (about $180 million) let alone as-built drawings.
The last misconception is that, as any deliverable, quality has its lifecycle. It does not. Similar to know-how, quality is ubiquitous and transcends all the disciplines, the project phases, and all the projects. Even the equipment procurement starts with quality in mind. Example below is a comparison of progressive payments terms offered by the biggest pump manufacturer and a quality-minded EPC contractor. The contractor's version has subtle differences, which drastically reduce the risks of the inferior quality as its criteria are interwoven into a fabric of the order tracking.
Table 1A Pump supplier progressive payment terms example
% | Milestone |
---|---|
10 | downpayment, upon order receipt |
20 | upon submittal of outline drawing |
30 | upon receipt of casing castings at manufacture's works |
40 | upon notification of readiness for dispatch |
Table 1B Progressive payment terms offered by client
% | Milestone |
---|---|
10 | downpayment, upon approval of the following documents submitted by the supplier: 1. pump specification review, 2. time schedule, 3. inspection and test plan |
20 | upon approval of the following documents: 1. GA drawing 2. CS drawing 3. coupling drawing 4. mechanical seal drawing 5. performance curves and startup torques 6. rotodynamic analysis, 7. test procedure |
30 | upon approval of NDT inspection of casing castings and certificates of material compliance at foundry site |
35 | upon the pump test results approval and pump delivery ex-works |
5 | upon full document package delivery |
The cornerstone question is
How to build minimum viable QMS that really adds value to mega-projects execution?
First, we need to depart from conventional definition of QMS as a technique used to explain to employees what is required and to influence employee actions to complete tasks according to the quality specifications. Instead of "Explain & Influence" new IT-driven QMS shall set clearly measurable objectives for Quality Planning (QP), Design Verification & Validation (V&V), Quality Assurance (QA) and Quality Control (QC). It shall supervise and guide the business processes to comply with the project requirements set by the client.
Scary task, isn't it? It has shockingly simple solution - the only input that such QMS needs is the FEED data.
FEED stands for Front End Engineering & Design. It produces full information on the equipment ordering and defines the exact scope of detail mechanical, electrical, instrumentation and control design. FEED substantiates the plant guaranteed functionality and reliability, the project timetable and the budget and substantially decreases the project risks and contingencies. Crenger creates FEED just in 40 man-hours regardless of the mega-project size. FEED is a solid basis for QMS scope and budget estimation and resources allocation.
Quality Planning (QP)
QP answers a single question – what shall be done to deliver the quality promised.
A key to a successful QP is the project risks identification framework. Its basics is extensively covered in "Handling Megaproject Risks" article. (ISO 9001 standard is silent about quality risks nature and identification.)
Two points are worth reiterating. First is an inherent and constantly moving gap between the project requirements and the contractor expertise, intended to be "filled" with innovations. They are necessary to achieve better performance, to better the chances of winning the project. So any project is a mix of technologies ranging from conventional to commercially unproven. The second is the project team adequacy and availability to the project tasks (executed in-house or in collaboration) to be re-assessed each time due to turnover of the company staff and collaboration partners. Both points contribute most to the QP scope.
Crenger introduces a group of Key Performance Indicators (KPI) assessing engineering expertise of the company, design conditions mismatch (comparing to the project requirements), and a previous experience strength. These KPIs are applied before any project activities.
The second group of KPIs analyzes the results of FEED executed during bidding. These KPIs reflect the quality of the team performance; they take into account the number and nature of inconsistencies found during auto-auditing of FEED solutions.
These constantly updated KPIs give clear picture of the points of concern, which may be easily translated into QP new procedures for both project deliverables and processes, new assignments and even opportunities!
Design Verification & Validation
Design validation can be expressed by the question "Are you engineering the right plant?" and design verification shall answer the question "Are you engineering it right?"
At the core of the design verification should lie internal auditing of the data framed into engineering reports, technical and functional specifications of equipment, systems and processes. Unlike documents, this data possesses a new inherent quality called traceability.
In real life verification is paid little attention even in big companies due to vague understanding of its practical implementation, resources constrains, and time limitation. In worst-case scenario lack of verification may turn into major cost and schedule driver for a project.
Crenger automates data and traceability auditing by introducing the described below frameworks.
Components and Systems Integration Verification
A plant is a collection of subsystems, each being a collection of end-items. In similar way the plant requirements may be decomposed onto the subsystem ones, which, in turn, may be translated into the end-item requirements.
How to verify and record the goodness of subsystems and components match, for example, in the desalination project of 150MLD having the following metrics (Table 2)? This task is beyond any EPC contractor, big or small. Then does he/she care about subsystem interfaces analysis?
Table 2 150 MLD desalination plant metrics
|
|
Crenger models the project as tree structure; its root node – project – may be expanded into subsystems and end-items, the requirements tree mirrors the first. The links between the end-items are where the magic begins.
Information Consistency and Sufficiency Verification
Crenger links information sufficiency to the main phases of the project – engineering, detailed design, etc. Any transition to the next phase triggers additional massive auditing of the information; data inconsistency, pending or outstanding issues, unfinished tasks may block the progress.
Crenger auto-runs data auditing daily. It covers P&ID, PFD, Plant wiring, design goodness for requested service, fluid and construction material compatibility, documentation packages, and whether project execution sequence is not broken. Examples of the design auditing tasks are checking the distance between the magnetic flow meter and the variable speed drive, checking that polypropylene is not used for hypochlorite service, checking that butterfly valves sized above 8 inch are equipped with gearbox, etc. Currently pre-built library includes over 90 auditing tasks. Extensive metrics (ranging from equipment pieces with "pending" status to number of revisions done to work hours spent) gives instant project picture and the progress done.
Crenger differentiates information according to the credibility levels of "pending", "for information", "for construction", and "as built" as inadvertent mixing of two- and more- levels leads to massive rework and project schedule slips.
For example, general assembly drawings obtained with quotations ("for information" level) are sufficient for starting Mechanical Design, but not enough for completing it – "for construction" level is required. The same is true for internally generated flow of information; its both levels ("for information" and "for construction") are produced and consumed concurrently.
Outstanding Issues Tracking
The present practice is to discuss the problems at the daily or weekly design reviews - prioritize and assign the problem to a staff member for analysis, and establish a due date for its resolution. The burden of the problem follow-up is often assigned to the process engineer inundated with hundreds of other problems. It leads to buildup of forgotten issues, the problem biased prioritization, resolution of the same problems twice, and escalating time losses.
Crenger logs and tracks identified problems, and ensures that they are corrected. It periodically reports on problem status and process metrics through email alerts, and auto-assigns problems to predefined specialists (e.g. the pump expert). It notifies the assignee of the new assignment and the due date. The recorded issues may be easily searched through, used for trend analysis related to number of problems detected, rate of problem correction, source of the error (e.g., bad process, unclear requirements, poor testing, etc.) and identification of design areas where problems occur most frequently.
Quality Assurance (QA)
QA's objective is preventing defects in deliverables to avoid rework.
Construction surveys evidence that 70% of the process project success is defined by the equipment procurement. Therefore, by far the largest part of the quality "value" the process project inherits from the purchased equipment designed and built by original equipment manufacturer (OEM). Naturally, QA shall address OEM first.
OEM Screening
Vendor screening is aimed at creating a pool of OEMs producing equipment matching the project conditions. For example, the "desalination pump" category shall include only high-efficiency pumps using materials compatible with seawater or brackish one. This screening is based on web search and studying the OEM website materials.
Crenger offers OEMSE - an original equipment manufacturer (OEM) search engine. Unlike many general-purpose engines, it uses technical terminology describing the construction and the process in which the equipment searched for is used. The engine gives you a hint for most popular selections. In addition you may score your past experience with particular manufacturer (from full satisfaction to complete miss). In future OEMSE is planned to extend this engine to the engineering services providers.
OEM Prequalification
The second step is Qualifications Based Selection (QBS) of vendors for complex systems, custom equipment, engineering services, inspections and tests, etc. (QBS is identified as the global best practice across many industries.)
Crenger offers OEMSUV application. It surveys and rates OEMs on generic non-price attribute information and selects the top performers. OEMSUV collects and processes the vendor data covering a broad range of subjects like company management, quality system, product design and development, handling nonconformities, sub-vendors selection and risk management.
OEM Relationship Management
OEM relationship is a risk source by two reasons. The plant general warranty terms are signed long before negotiation of the warranties with OEM. Differences in warranties may be big enough to lose the project. Secondly, the end-item requirements may not be met by the products on the market. Product customization is a commonplace today. Customization requires deep understanding of the client business, which comes with a feel of partnership and – whether you accept it or not - open access to the past tenders database. It is a starting point for supplier performance improvement. You may learn more about Crenger tendering framework here.
Target Prices Verification
The practice of getting the lowest bid from prequalified vendors and engineering services providers has its pitfall: current tough competition and low revenue margins in industry leave the manufacturer no other choice then to cut on QA/QC expenses.
This serves neither manufacturer nor user. I witnessed a case where a very reputable manufacturer without prior notice to the client handed over machining of casings to inexperienced subcontractor. As a result four out of nine 5000 kW pumps had defective casings beyond repair. The disaster followed: commissioning of the pumping station was delayed by a month, the manufacturer reputation being badly damaged. To avoid such situations, negotiating prices shall be slowed down to a pace once you cross the line of the target price - your conservative estimate based on the prices for similar items available in the company database, current tariffs of the manpower, and construction material prices.
Crenger PRIGE plugin is an application for recording, retrieving and comparing the prices for the equipment pieces and systems. These reference price database is equally important for the project engineers and for OEM. The first will have a solid basis for the project costs estimation, while the latter - an entry-level price target not to miss. To promote free exchange of equipment prices and make the user feel at ease, all records are anonymous - tied neither to the user nor to OEM.
Equipment Inspections and Tests
The next point in QMS is the equipment manufacturing inspections and tests (commonly bundled as Inspection and Test Plan (ITP) for each procured item and subsystem. Its intended use is to detect any potential nonconformities sources on equipment before its manufacturing and shipping to construction site. It is a list of what and how to test and inspect to ensure the operation and safety parameters are met as designed. As ITP scope substantially affects the project schedule and costs, it should be binding part of the project technical and commercial offers.
This obvious requirement has never been implemented in the mega-projects I participated. Why? Because it's hell lot of a work. Crenger auto-generates the ITP bundle documentation in no time. Below is a snapshot of the ITP framework interface.
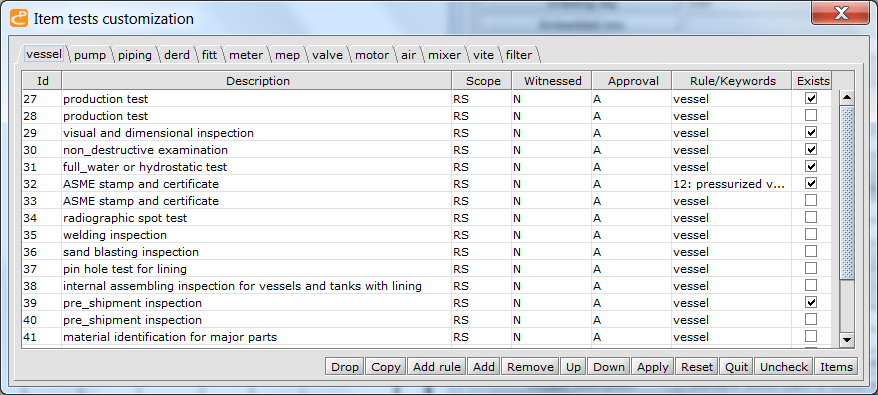
For inspections and tests recording and reporting Crenger offers EQUINS application. It allows one to quickly create inspection and testing report and share it with the project team on the web and track easily outstanding issues, or view the project inspections progress. Download inspection report sample here.
Quality Control (QC)
Unlike QA governing project processes, QC covers project deliverables. It is a "check-in/out" control of systems and items for defects and nonconformities – deviations from the project requirements. QC gauges, monitors, and tests quality, and summarizes negative results in nonconformance reports (NCR) and "lessons learned". Beyond any doubt, the core QC activities are Document Control and Project Completion and Commissioning (CC). Its general tasks and content are described in Norsok standard.
Document Control
Globally distributed manufacturing of equipment and its parts demands higher standards of QA from both OEM and the project contractor. In mega-projects this requirement merely triggers a paper waterfall: only the QA documentation package of the large-capacity pump includes more than 35 items!
Their approval is a task of Document Control. Its most difficult part is the submittals list compilation for P&ID items - crucial task beyond human capabilities. Submittals lists are a binding part of the project technical offer (together with the Quality Plan and ITP).
Crenger auto-creates the submittals list for each procured piece of equipment. OEM uploads these submittals directly to the project folder.
CC Inspections and Tests
CC is a well-shaped discipline focusing on
- Inspection of equipment installation for compliance with the contract
- Equipment and operational systems start-up and operational performance testing
- Acceptance and turnover of equipment, systems, and facilities to operators
- Turnover of equipment spare parts and items, special tools to the operator
- Turnover of project documentation to the operator
First point is the hardest to pass merely due to a volume of work to be done. For example, over 8000 certificates (installation, assembly, cable connection, instrument calibration, pressure & functional test, etc.) shall be issued for a grass-root desalination project of 150 MLD. I do not remember any desalination project where this work has been done by the book.
Crenger auto-generates all Inspection & Test Certificates. Besides typical data, they contain excerpts from P&ID and the plant layout showing location of the item in question. Sample certificates may be downloaded here.
Crenger verifies that the pressure and functional tests scope to be defined and shown on P&ID before starting detail design as it may additionally require installation of blinds on piping and vessels, provision of the overflow capacities and isolation valves. If inspections and tests are outsourced to experienced subcontractors, such certificates become part of the purchase order and the warranty terms are auto-added to the content.