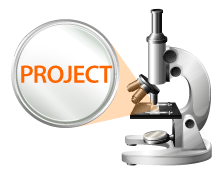
Unlike engineering design validation encompassing tests and inspections, the P&ID validation covers engineering specifications for the P&ID elements as a single whole - the plant. It should meet budget, safety, operation, and maintenance requirements, to say nothing about engineering errors. Each specification is a collection of some attributes and parameters. Part of them is the customer's input, others are the designer's selection.
The metrics obtained with the PlantDesigner software show that for a small mega-plant of 100 MLD capacity the total number of attributes and parameters is about 30000. As in conventional engineering, all of them are set manually, this figure defines the extent of the P&ID validation.
It is a stressful and error-prone assignment as the attributes and parameters in question are set in different types of documents linked by the P&ID item tags not easy to memorize.
Seven points change the digitized P&ID validation process.
- All the validation data is retrieved by the button click
- The bigger part of the attributes and parameters is auto-generated and does not require any validation
- There is no need either in the process and control tags validation as the tags are selected and continually synchronized automatically
- Matching between the P&ID items is validated automatically during the engineering in real-time
- Valves and lines are sized automatically - no need for validation of the piping class for material and ratings
- Consistency between reports such as instrument index, control philosophy, and the line list sizing calculation are maintained automatically
- Digital tags in reports are hyperlinked - when pressed, the full information about the object pops up
- The valve material shall match chemical fluid
- The kinetic energy of a fluid in piping shall be below safe limits
- The VSD size shall match the motor size
Crenger.com subdivides the P&ID validation rules (about 90) into 6 areas.
- data consistency
- design sequence
- process design
- electric design
- control design
- mechanical design
The design sequence type addresses the attempts of violating the natural flow of engineering. Examples are expediting the mechanical design without the equipment arrangement drawings, starting procurement without a sufficient database of the equipment suppliers or purchase packages created, etc. Discipline-sorted rules are just hints on the abnormality source indicating where might be the reason.
Rules are sorted by a possible impact on the design in case they are broken. Crenger introduces the following design impact classes.
- FATAL - erroneous data
- ERROR - design miss
- GEP - deviation from good engineering practice
Examples of the FATAL abnormality - missing connection between P&IDs, linking the meter to the wrong piece of equipment, wrong fluid pressure, an instrument not wired, the P&ID item without the catalog id, pressure gage for aggressive fluid without diaphragm seal, etc.
Examples of the ERROR abnormality are erroneous quantities of procured equipment, a meter specified without equipment housing it, the meter alarm not linked to a registered fault, action or interlock, a meter without hook-up drawing, piping not designed for full vacuum, a motor or a pump not equipped with meters, a motor and a VSD differing in power voltage, etc.
GEP deals mostly with design optimization or the industry's internal standards.
Examples of GEP abnormality are a gauge intended for frequent measurements, a control loop meter without registered fault, a meter inadequate for troubleshooting the equipment fault, a magnetic flow meter too close to VSD, a motor underrated for working with VSD, etc.
To apply the impact class and the rule to the P&ID item crenger.com uses special selectors - P&ID crawlers. They search for the P&ID items matching the rule and validate them. If auto-correction is activated, the validator resolves the abnormality.
Smart validators are subdivided into hardcoded (HV) and soft-coded (SV). HV cannot be changed or removed by the designer. The SV ones are intended for the collection extension using the client interface. SV is an off-P&ID item with parameters and attributes set as conditions.
HV and SV are used, firstly, for search and, secondly, for the rule application. Conditions may be set by using the graphic interface or creating an SQL query. Here SQL stands for Selector Query Language. Below are sample queries demonstrating the SQL structure.
- set voltage = 'low 2' where output rate > 250 and output rate < 1000 unit = 'KW'
- assert standard = 'NEMA' if voltage = 'low 1' and size > 250 and size < 1000 unit = 'KW'
- for design = 'vertical turbine' use rpm < 1000