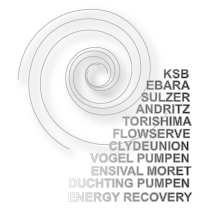
Digital Twin (DT) is a real-time digital "image" of the physical asset state and performance. To be useful, it should be compared any time with the initial image created by the designer during the plant engineering.
This initial image is a collection of data, process models and validation rules setting design limits. As well it defines the rules of the plant digital scanning.
The images comparison starts from the collected data normalization. It is the essence of the equipment predictive maintenance (PM). Examples are PM plans for reverse osmosis membranes, filters and pumps.
Today the power industry is indisputable leader in the DT implementation. Results are higher efficiencies, longer asset lives and the customer's satisfaction. Should the desalination follow suit to become affordable? I think three cases below are a good reason to say it definitely should.
Plant Warranty
Recently I reviewed the warranty documents of the 400 MLD SWRO desalination plant. Amongst many others, they include 365 printouts of the SWRO membranes array performance data. The enormity of work done is just shocking. In practice it is hardly of any value, as the membrane conditions were not paired with the pumps group performance. The latter was not included in the warranty at all. The reason was simple - the pumps were from different manufacturers, each one refused to extend its warranty to the pumps of the competitor. The same was true for all other equipment pieces which performances depend on the pumps.
DT replaces the paper warranty. As DT catches any deviation from the initially warranted state, it make predictive decision-making a standard. The plant operation becomes transparent to the manufacturer. Transparency is a basis for much better warranty conditions.
BOO Projects Profitability
By the same time I had a meeting with the company which prepared for the participation in the BOO tender for big desalination plant. To avoid disaster like in the Hyflux case, the profitability of the BOO mega-projects over the life cycle shall be meticulously predicted. It was the number one problem raised by the company. The core of it is how to predict and compare the plant actual performances over the time of the year under the varying temperatures and salinities of seawater, hourly tariffs and the requested monthly productions of product water. Design reliability and maintenance levels shall be addressed as well.
DT naturally targets this problem as it starts from the physical processes modeling judging by GE experience.
Renewables & Desalination Senergy
Solar-powered desalination gains momentum. An important milestone is the ENAPAC project in Atacama, Chile. It contains a 227,232 m3/d reverse osmosis desalination facility, powered by a 100 MW photovoltaic plant. To ease the problem of matching the water consumption with the solar energy diurnal variations, the designers equipped the plant with the buffer capacity of 600,000 m3. The required investment is pegged at $500 million.
One cannot help noticing that the huge buffer capacity is an attempt to solve the said problem without deep analysis of ecosystem functionality, reliability and maintainability. It is what DT is intended for.
How to start building desalination plant DT from scratch?
The first step is to create the hydraulic model of the plant linking the energy consumption, pressures and flows to the plant production. The model shall describe the real equipment available in the market. Here the focus is on partial performance and the preferred operation range. Successive steps are to enhance this model with all other aspects - mechanical, electrical, chemical, material, economic and statistical.
Crenger.com already began this journey with PumpStudio platform.
It is a collection of applications needed to engineer the desalination process, select and rate the equipment and model the plant actual performance at different conditions (like seawater temperature and salinity variations over the tine of the year, hourly electricity tariffs, the water consumption loads).
CREPSE is process-focused; it gives answers even if only the pump capacity and the process description (like flushing or backwash) are given. CREPSE shortcuts the pumps selection from weeks to a couple of minutes.