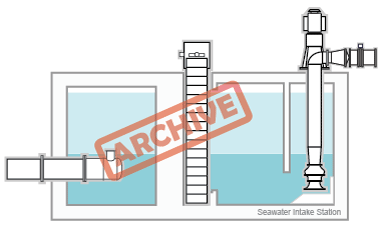
Poseidon started its desalination business because of the opportunity to reduce its costs by tapping into the power plant intake systems. It succeeded in Carlsbad, but failed in Huntington Beach.
Does this mean the end of story? Is intake-less concept worth serious consideration at all? The answer is not that simple.
I was never satisfied with the intake systems I designed in the past. They seemed to me too far from perfection every engineer is looking for.
It starts from a possibility to smoothly extend the production rate after commissioning following the water consumption growth. Nearly all desalination plants go through this process. Extensibility is a litmus paper of the plant design maturity.
Modern intake designs are not extensible due to massive concrete sump below the ground level.
High CAPEX – above 10% of the plant's one – makes intake oversizing not attractive. Besides it creates volumes of stagnant water accelerating biofouling growth and corrosion of standby equipment.
Deeper intakes as another way of oversizing is hardly an option too as their CAPEX grows exponentially with every meter of the sump depth.
(There is no definition for "deep intake". One may assume that it is a case when the number of bidders for intake equipment (screens, pumps) drops to 2 – 3. To the best of my knowledge, it happens when the depth is over 15 meters.)
What makes them look especially clumsy is rotating band screens and vertical pumps. It is hard for engineering mind to accept the fact that only 10 – 15% of the screen surface framed into expensive super-duplex is actually used for water filtration.
Lengthy column pipe dominates in the vertical pump price and raises obvious question – are we buying a pump or a pipe? Besides it introduces high uncertainty into the pump roto-dynamic analysis which makes its results dubious. In one of my projects this analysis produced a succession of 7 explanations of the high vibration in descending order of probability. Only fourth hit the target. First three failed.
Another problem of pumps associated with deep intakes is dry-bearing start. Too many starts kill the bearings. Quenching prolongs their life to 3 – 4 years. Replacement requires crane and extra space for maneuvering – extra design constraint.
Intake sump geometry is not a designer choice, it is optimized to match the intake piping length. Environmental constraints, shallow sea and high tides may stretch it to 2 – 4 kilometers.
In hydraulics parlance this piping is called "suction piping"; it features low water velocities (below 1.2 m/sec) and works under external pressure.
Low velocities trigger quick fouling and pressure/level drop rise, while external pressure contributes to higher prices especially at big diameters (over 1.6 m).
If the water level is below some point corresponding to the pump minimum submergence, the pump performance becomes unstable.
Unpredictable fouling rates make the intake designer specify the piping redundancy in excess of 75%. This costly redundancy may take different forms – lower than recommended water velocity or/and the Hazen-Williams coefficient values.
Design uncertainties and assumptions are a good reason to consider the intake as a project risk source. (To mitigate it we have two "helpers" – "Pump Intake Design" from Hydraulic Institute and CFD analysis. The latter may cost you US$ 20000 – 35000.)
Too many design constraints and inevitable customization turn intake into a bottleneck of many desalination plants. Can we handle this challenge?
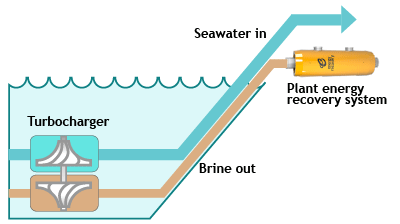
When one door closes another opens. Sometimes a possible solution is just around the corner. It is called Drop-in Turbocharger. It is installed near the intake head and pumps seawater using backpressure of the brine discharged from the energy recovery system of the desalination plant.