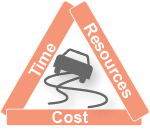
By McKinsey, investments in infrastructure projects (water, oil & gas, energy, pharma, chemical) will double in the next 12 years. Bigger projects will dominate despite the current disastrous statistics saying that 98% of megaprojects suffer cost overruns of more than 30%; 77% are at least 40% late.
The first point - costs overruns - I touched upon in my post "Why Bid/No-Bid analysis matters". Below is my selection of key problems contributing to process megaprojects unrealistic scheduling. An example of mega-process is seawater reverse osmosis desalination, oil cracking, or LNG. All of them have a common roadmap – Piping & Instrumentation Diagram (P&ID).
Scheduling targets are wrong
It is a well-known fact that the success in the process projects mostly depends on timely delivery of equipment pieces and subsystems. Hence, Project Schedule (PS) shall be pivoted around the purchase orders and the equipment inspections.
Each purchase package handles the P&ID items of the same class and similar lead time category. It includes general requirements specifications, auto-generated datasheets in Excel, purchasing terms and conditions, and a payment scheme rooted into Inspection and Test Plan.
I do not remember a single mega-project where this simple and obvious requirement has been implemented; PS does not explain how equipment pieces are wrapped into purchase orders. Instead, typical PS reflects the process engineering sequence in sizing the P&ID items. Packaging items into purchase orders is a task of procurement personnel not involved in the project scheduling.
Duration-type activities dominate, making PS experience useless in future projects planning
It is convenient to present the work load of any task in figures easily understood by all stakeholders – in hours or days – without taking into account available resources, skills, and the project size.
If you ask the experienced water treatment engineer how much time is needed to prepare P&ID sheet of A3 format, the most probably answer would be 50 - 150 hours regardless of the process complexity and novelty, number of P&ID items and specifications to handle.
This bad practice makes it impossible to analyze the project schedule retrospectively with the aim of fine-tuning the existing practices and gaining more insights for future projects.
Duration-type activities dominance is a direct consequence of skipping the FEED phase of the project development aiming at the project scope definition.
Automation & Control (A&C) is on the project critical path
Automation & Control is not a priority of the EPC contractors; in most megaprojects it is outsourced and neglected by project managers (due to small percentage in the total expenses).
Being always in the wake of the process and mechanical engineering, it gets the blow of all scope changes and costs cutting. In addition, the mere boilerplate A&C specifications rarely meet the client expectations. This, in turn, makes A&C one of the project risks today.
How serious is this problem? In 2008 I participated in a megaproject where A&C costs overruns hit 500% (!) - about 50% of the engineering budget - and caused several-month delay.
This attitude increases the distance between so-called mechanical completion of the project and the project acceptance by months. Moving to wireless devices will definitely alleviate the gravity of the problem, but will not solve it – all the A&C activities shift is needed to the beginning of planning and design of a project.
Different culture is needed to move the focus from the process operability (defined by mechanical design) to the process controllability and remote visibility – paramount requirement of the digital age.
Time and money constraints are not inculcated into mindset of the process engineers
In 2007, on my question to the process department manager why the software was not in use, she honestly answered that time was not important - the process engineer should learn to size equipment manually.
Now we live in different age when the fast beats the slow, and the definition of any business model starts from words "holistic" and "diversity".
Without collaboration with the process engineer, the project scheduler is unable to assess the interdependencies and the impact of P&ID - rooted activities on PS critical path or chain.
Inability to analyze force them to turn PS into "todo" list hiding the true project picture. Activities like "Update of..." and "Correction of..." become normal practice in the environment with broken logic of the project execution.
Zero IQ of the project scheduling software is a bottleneck
Existing PS software is a dumb data aggregator without any idea about the data validation and business processes in question. Attempts to analyze them tumble over the GIGO principle: garbage in, garbage out.
Despite the dominance of P&ID items in the schedule activities no PS software knows how to read P&ID, PFD, Plant Wiring, or One-Line Electrical Diagram.
Lack of bi-directional navigation between the PS subjects (like valve or pump) and the PS activities on subjects (like the pump inspection or the pump test approval) is the main reason of PS inefficacy.
Manual synchronization of PS with engineering and procurement data updates is error-prone, time-consuming and always late. Successive synchronization of resources falls in the same pitfall.
Schedule analysis & optimization are not done
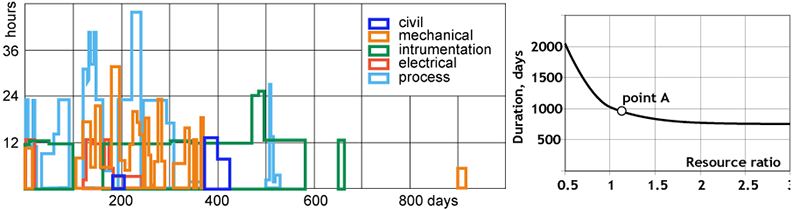
In a nutshell, the scheduling tools shall know how to build the following 2 charts. First describes the resources daily loads distribution over entire duration of the project. This chart is the basis for resources naming and load synchronization over all currently executed projects.
The second chart describes the project duration sensitivity to resources availability. It shows, for example, that there exists a magic point A after which adding new resources does not contribute to the project time shrinking.
The third basic wish-task of scheduling is resources levelling - finding optimal ratio between different resource categories like process, electrical, instrumentation and control, mechanical and others. What I mean is this sample table. It shows that adding, for example, the process engineer will shorten the project duration by 19 days! (Another interesting detail in the figure right above the table is dotted circles - the order issue activities.)
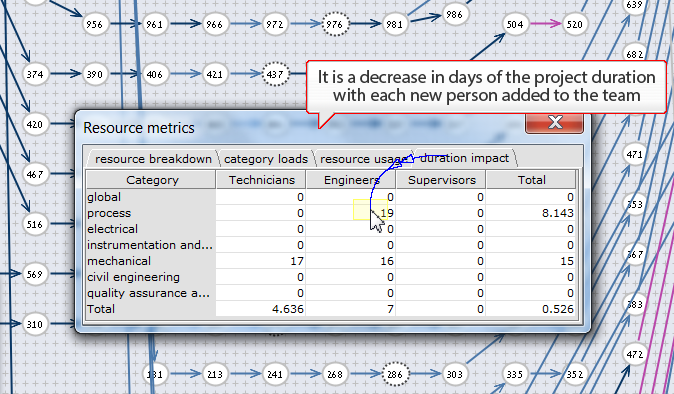
Scheduling tools do not understand risk categories
If we accept that any project schedule is mathematically described by a unidirectional graph with a single point of entry (project award) and that of exit (plant acceptance), then first basic axiom would be that dangling (not linked) activities pose a risk and shall not be allowed in megaproject. This requirement has been never implemented in life by two reasons.
- FEED is skipped and project execution goes concurrently with the planned (!) scope creep - continuous adding new tasks.
- Schedulers do not understand the project logic and the consequences of dangling activities.
As scheduling tools are not linked to engineering and procurement software, associated risks cannot be transmitted automatically to the schedule. So such wish-task as the impact assessment of the OEM market match to the project on PS is beyond the scope. (Example is 6MV/60Hz pump for the Carlsbad SWRO desalination project, which did not exist in the market by the time of the project award.)
Activity scope and its costs are left out of scheduling entirely
Simple logic tells that the project scope and costs shall be sums of all the project activities scopes and costs accordingly. Naturally, these micro-scopes and micro-costs shall be put into the schedule activities. Overloaded with the scope and costs information, such PS becomes a solid basis for planning the project financing.
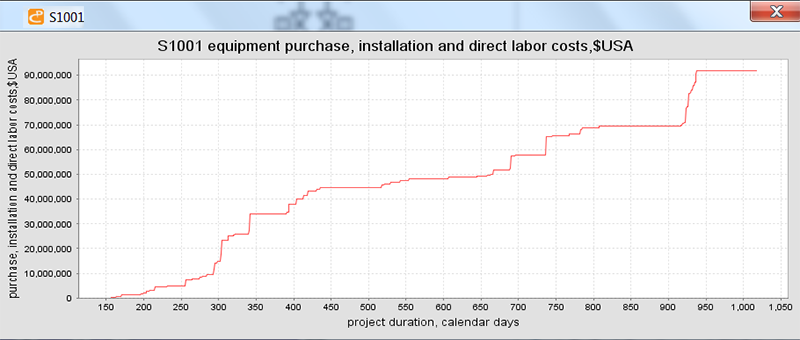
In other words, the activity scope and costs are as important as the activity work load or allocated resources. It is never done in practice as this process is not automated and extremely time-consuming, and bad old practice of ball-park figures is still alive.